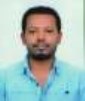
Tesfaye Meseret Abebe
Otto-Von-Guericke University, Germany
Title: Aerodynamic design and analysis of a small scale wind turbine Rotor blade
Biography
Biography: Tesfaye Meseret Abebe
Abstract
The basic principle of a wind turbine which converts wind energy into electricity comes from the lift force produced by the flow of air through the rotor. In this paper the aerodynamic profile of a small scale wind turbine rotor blade is designed based on a surveyed meteorological data for a site location called (Aysha dawale, ETHIOPIA). To design this blade the blade element momentum theory (BEM) is used, and based on this theory a code is developed using MATLAB to facilitate the design process. Types of airfoils which are used in the small scale wind turbine industry were investigated and compared based on optimum aerodynamic performance and thickness to chord ration for structural stability. According to this criterion the NREL airfoil families suited for small scale wind turbine blades in the range 2-5m blade length are selected and simulated using XFOIL to be an input for the design. After deciding the above initial parameter (airfoil type), the essential geometrical parameters such as twist angle and chord distribution along the blade span is optimized. The final values of this parameters decide the amount of power that can extracted from the wind, which is defined by the power coefficient.
An optimum power coefficient result requires optimizing the twist angle and chord distribution. In this design the chord distribution is designed to follow a linear shape tapering from the root to the tip of the blade. The remaining parameter (twist angle) is optimized using gradient based optimization technique coupled with the BEM program coded in MATLAB. This optimization technique is an automated process which receives variables to be optimized from the MATLAB solver (fmincon) and feeds through the BEM code, while the BEM code simultaneously access the simulated data’s of the airfoils and validate the optimum variables when a maximum power coefficient result is achieved. Based on this design technique a blade is designed for wind speeds which occurs most frequently weighted by the weighbull distribution. Simulation results of this design using QBLADE yields a minimum capacity of 1.4KW: at 4m/s wind speed, 50RPM rotor angular speed and a maximum capacity of 12.8KW: at 8m/s wind speed, 80RPM rotor speed efficient wind power conversion capacity is achieved. Further increasing the rotor angular speed to 200RPM increases the power capacity to 94.3KW at 16m/s wind speed, but according to the wind speed distribution in the selected region, for an average annual wind speed of 8.3m/s the rotor angular speed should be no more than 80RPM for efficient power conversion purpose. Within this bound the turbine can achieve a rated output power of 12.8KW.